How is AI Transforming the World of Financial Digital Marketing?
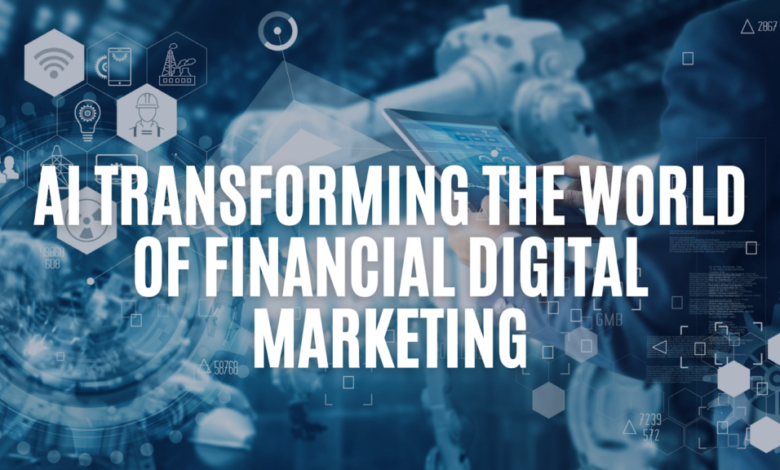
Artificial intelligence is a game-changing invention that has greatly impacted all facets of the industry across industries. Learn how it is changing The World of Financial Digital Marketing.
AI is shaping digital techniques by the ability to gather data, interpret it, apply it, and then learn from it. If it advances, so will businesses’ willingness to use it to develop digital marketing campaigns and provide useful consumer feedback.
It has been suggested that artificial intelligence would be essential in future digital goods, especially in the field of digital marketing. From the film “The Matrix” to Google AI, from the amusing and astute Siri to Tesla’s self-driving vehicle, more and more companies are incorporating AI into their digital marketing strategies. The future of TD Media LLC digital marketing is being shaped by artificial intelligence.
What Exactly is Artificial Intelligence?
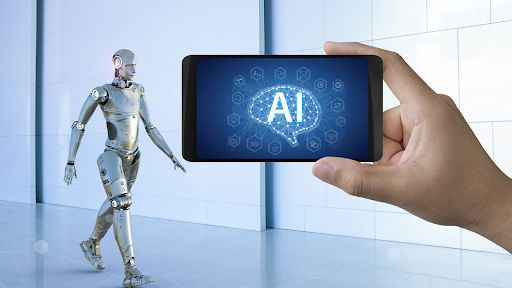
According to Wikipedia, “artificial intelligence” refers to robots and algorithms that emulate “cognitive” tasks associated with human brains, such as understanding and problem-solving.
It is a branch of computer science that seeks to explain the nature of intelligence in order to create a new intelligent system that thinks, reacts, and executes tasks based on the data feed into it, much as humans do. Robotics, voice recognition, image recognition, natural language analysis, problem-solving, and other tasks involved with AI are highly advanced and advanced.
It is possible that in the future, the technical goods brought by artificial intelligence will be the “shell” of human knowledge. AI is not human intelligence, but it does think like one and can even outperform it.
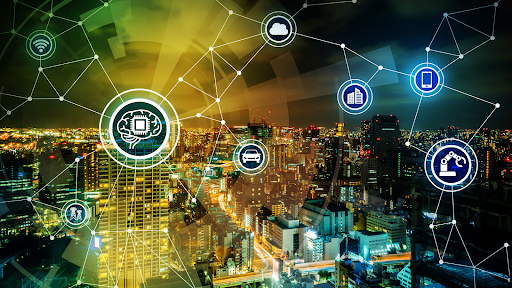
The Link Between AI and Digital Marketing Agency
Previously, advertisers were reluctant to incorporate artificial intelligence into their business campaigns. However, several popular companies have embraced it and use it in their ads, with brands such as Amazon and Spotify successfully using AI programmed.
Amazon, for example, uses AI to offer customers only related items based on recent searches, orders, and views. This will raise the chances that a shopper will make an original purchase or become a return customer, since the customized service is strongly desired.
AI in Life Water Media digital marketing is now a possibility, including a variety of advantages and choices. Let’s look at how we can use artificial intelligence in digital marketing agency.
How is Artificial Intelligence (AI) Changing Digital Marketing?
AI is revolutionizing digital marketing with its ability to gather data, interpret it, apply it, and then respond to it. Because of its ability to make data-driven decisions easily and reliably, AI will become more relevant as the amount of knowledge on future users increases. Here are some of the ways AI is influencing digital marketing:
1. Recognize and Evaluate
Customer relationship management (CRM) is a corporate philosophy that develops a customer-centric approach to business by optimizing customer information gathering and filtering valid information.
As CRM, AI, and big data technologies are merged, they will optimize the aggregation of consumer knowledge from various sources, generate reliable feedback for potential markets, and identify users’ interests, allowing businesses to decide the most effective campaign approach.
2. When AI and AR/VR Work Together
When AI meets emerging visual innovations like AR and VR, it creates a new consumption experience.
3. Electronic mail advertisement (Email)
AI enables advertisers to personalize email marketing strategies based on customer preferences, allowing advertisers to deliver emails prompted by specific behavior. This allows them to send relevant emails to consumers’ inboxes, with subject lines, product tips, and messaging all selected based on their behavior.
3 Ways AI Has Transformed The Financial Digital Marketing
1. Risk Assessment:
Since the very foundation of AI is learning from previous data, it is common for AI to excel in the Financial Services domain, where bookkeeping and records are second nature to the company. Let’s look at credit cards as an example. Today, we use credit scores to determine who is and is not qualified for a credit card. However, categorizing individuals as ‘haves’ or ‘have-nots’ is not necessarily effective in industry.
2. Fraud Detection and Management:
Any company strives to reduce the risks that surround it. This is true also for a financial institution. Since the loan you get from a bank is essentially someone else’s income, you are therefore paid interest on deposits and returns on assets. This is also the reason that banks and financial institutions take fraud so seriously.
3. Financial Advisory Services:
According to the PWC Study, more robo-advisors are on the way. As financial institutions face will pressure to lower their commission rates on individual investments, computers can do what humans do not: work for a single down payment. Another rapidly developing area is bionic advisory, which incorporates computer equations with human intuition to offer options that are much more effective than their individual components. Collaboration is important.